Wages are one of the major portion in the total cost of production. There is always a chance of fraud in wage payment. Therefore, an effective administrative and accounting control system must be implemented by the management to minimize fraud and to keep the labor cost minimum. As already stated, a number of departments are set up for the effective utilization of labor force and its proper accounting and controlling. These departments are required to work in a coordinated manner and to support the management in controlling labor cost by recording...
Sunday, 30 May 2010
Differences Between Piece Rate System And Time Rate System Of Wage Payment
Posted on 21:51 by Unknown
Following are the main differences between piece rate system and time rate system.1. MeaningPiece rate system is a method of wage payment to workers based on the quantity of output they have produced. Time rate system is a method of wage payment to workers based on time spent by them for the production of output.2. Nature Of PaymentPiece rate system pays the workers according to the units of output produced. Time rate system pays the workers according to the time spent in the factory.3. EmphasisPiece rate system gives emphasis on larger quantity...
Saturday, 29 May 2010
Concept And Meaning Of Time Rate System Of Wage Payment, Its Advantages And Disadvantages
Posted on 23:29 by Unknown
The time rate system is that system of wage payment in which the workers are paid on the basis of time spent by them in the factory. Under this system, the workers and employees are paid wages on the basis of the time they have worked rather than the volume of output they have produced. Hence, according to this system, wages are paid on hourly, weekly or monthly basis. Under time rate system, the wages earned by a worker is determined by using the following formula.Wages Earned = Time spent(Attended) x Wage rate per hour/day/week/monthAdvantages...
Concept And Meaning Of Piece Rate System Of Wage Payment, Its Advantages And Disadvantages
Posted on 23:00 by Unknown
The piece rate system is that system of wage payment in which the workers are paid on the basis of the units of output produced. Piece rate system does not consider the time spent by the workers. Piece rate system is the method of remunerating the workers according to the number of unit produced or job completed. It is also known as payment by result or output. Piece rate system pays wages at a fixed piece rate for each unit of output produced. The total wages earned by a worker is calculated by using the following formula.Total Wages Earned= Total...
Concept And Meaning Of Wage Payment System , Its Importance And Essential Characteristics
Posted on 22:31 by Unknown
The system of wage payment is the method adopted by manufacturing concerns to remunerate workers. It is the way of giving financial compensation to the workers for the time and effort invested by them in converting materials into finished products. It indicates the basis of making payment to the workers, which may be either on time basis or output basis. The selection of the system depends on the type and nature of the concern and its products. The wage payment systems can be divided into two main systems as follows.1. Piece rate system2. Time...
Importance Or Needs Of Labor Cost Control
Posted on 22:14 by Unknown
The need of labor cost control arises to fulfill the following purposes.* Labor cost control is important to make economic utilization of labor force in production process.*Labor cost control is important to obtain maximum quantity of output with the least amount of materials and other resources.* Labor cost control helps to obtain better quality output with the least effort and time of workers.* Labor cost control reduces the cost of production of products manufactured or services rendered.* Labor cost control ensures the satisfaction of the workers...
Concept And Meaning Of Labor Cost Control
Posted on 21:59 by Unknown
Labor cost covers one of the major portion of the total cost of a product or job. It may increase unnecessarily due to inefficiency of workers, wastage of materials by workers, idle time, unusual overtime work and high labor turnover. Hence, the management should devise effective techniques for controlling labor cost to ensure maximum outputs of better quality at low cost through proper utilization of the labor force.Basically, management is concerned with controlling labor cost. Labor cost control involves such systems, procedures, techniques...
Thursday, 27 May 2010
Importance Of Labor Cost
Posted on 23:19 by Unknown
Proper study, analysis and control of labor costs are important to all manufacturing concern because of the following reasons.* Labor cost is main element of cost which covers one of the major portions of the total cost of a product or job.* Labor cost is more difficult to control as compared to material cost due to the involvement of human element.* Labor cost is affected due to a change in government policy and requirement of trade union.* Labor cost is adversely affected due to dissatisfaction , irregularity, inefficiency, idle time, high labor...
Wednesday, 26 May 2010
Types Of Labor Costs
Posted on 23:34 by Unknown
Like the labor, labor costs are of two types such as follows1. Direct Labor CostDirect labor cost is the amount spent by the factory for those workers involved directly in the manufacturing process. It can be measured conveniently and accurately on per unit of output basis. Direct labor cost can be identified and allocated to the specific job or process or product. It forms a part of the prime cost. The examples of direct labor costs are the payments made to the workers engaged in making table, printing a book and constructing a dam etc.2. Indirect...
Concept And Meaning Of Labor And Labor Cost
Posted on 23:09 by Unknown
Concept And Meaning Of LaborLike materials, labor is also one of the prime inputs of production system. All manufacturing concerns require the labor for carrying out their production activities. The labor consists of workers who are essential to convert materials into finished products. The workers operate machine and perform other tasks to help convert materials into final outputs.The labor can be either direct or indirect. The labor who is directly engaged in the conversion process is called direct labor and who is not is called indirect labor....
Sunday, 23 May 2010
Calculation Of Economic Order Quantity(EOQ)
Posted on 22:35 by Unknown
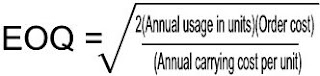
The economic order quantity can be determined in the following ways.1. Formula MethodWith the help of following formula, the economic order quantity can be calculated.2. Graphical MethodUnder this method, the carrying cost, ordering cost and total cost are shown on graph. It is based on the principle that the total carrying cost increases as the order size increases. However, the ordering cost decreases if the order size increases. The point at which...
Thursday, 20 May 2010
Concept And Meaning Of Economic Order Quantity(EOQ) And Its Related Costs
Posted on 23:33 by Unknown
Economic order quantity is also known as reorder quantity. Economic order quantity (EOQ) is a level of inventory where the total cost of holding inventory is at minimum. Economic order quantity is the level of quantity at which the cost of ordering will be equal with the storage cost of materials. In other words, the quantity of materials which is economical to be ordered at one time is known as economic order quantity. The total costs of materials consists of the ordering cost and carrying cost. While determining the economic order quantity, the...
Tuesday, 18 May 2010
Concept And Meaning Of Danger Level And Its Calculation
Posted on 23:08 by Unknown
Danger level is a level of fixed usually below the minimum level. When the stock reaches danger level, an urgent action for purchase is initiated. When stock reaches the minimum level, the storekeeper must make special arrangements to get fresh materials, so that the production may not be interrupted due to the shortage of materials.The formula for calculating the danger level is:Danger Level = Normal consumption x Maximum re-order period for emergency purchaseIllustration,Daily Consumption = 100 to 200 unitsMaximum re-order period for emergency...
Concept And Meaning Of Average Stock Level And Its Calculation
Posted on 23:01 by Unknown
Average Stock level shows the average stock held by a firm. The average stock level can be calculated with the help of following formula.Average Stock Level = Minimum Level + (1/2Re-order Quantity)ORAverage Stock Level = (Minimum Level + Maximum Level)/2IllustrationRe-order quantity = 2000 unitsMinimum Level = 500 unitsAverage stock level = ?Solution,Average stock level = Minimum level + 1/2 x Re-order quantity= 500 + 1/2 x 2000= 500+ 1000= 1500 uni...
Concept And Meaning Of Maximum Level And Its Calculation
Posted on 22:43 by Unknown
Maximum level is that level of stock, which is not normally allowed to be exceeded. Beyond the maximum stock level, a blockage of capital should be exercised to check unnecessary stock. The factory should not keep materials more than the maximum stock level. It increases the carrying cost of holding unnecessary inventory level. It is the opportunity cost of holding inventory.The maximum stock level can be calculated by using the following formula:Maximum Level = Re-order Level + Re-order quantity - (Minimum consumption x Minimum Delivery Time)IllustrationRe-order...
Concept And Meaning Of Minimum Level Or Safety Stock And Its Calculation
Posted on 22:24 by Unknown

Minimum Stock LevelMinimum level or safety stock level is the level of inventory, below which the stock of materials should not be fall. If the stock goes below minimum level, there is a possibility that the production may be interrupted due to shortage of materials. In other words, the minimum level represents the minimum quantity of the stock that should be held at all times.The minimum level is determined by using the following formula:Minimum...
Monday, 17 May 2010
Concept And Meaning Of Re-order Level And Its Calculation
Posted on 02:16 by Unknown
Re-order level is a level of material at which the storekeeper should initiate the purchase requisition for fresh supplies. When the stock-in-hand comes down to the re-ordering level, it is an indication that an action should be taken for replenishment or purchase.The re-order level is calculated as follows:Re-order Level= Minimum Level(Safety stock) + (Average lead time x Average consumption)ORRe-order Level= Maximum Consumption x Maximum Re-ordering PeriodIllustrationSuppose,Maximum consumption per day = 400 unitsMinimum consumption per day ...
Concept And Meaning Of Stock Level
Posted on 00:46 by Unknown
Stock level refers to the different levels of stock which are required for an efficient and effective control of materials and to avoid over and under-stocking of materials. The purpose of materials control is to maintain the sock of raw materials as low as possible and at the same time they may be available as and when required. To avoid over and under-stocking, the storekeeper must fix the inventory level, which is also known as a demand and supply method of stock control. In a scientific system of inventory control the following levels of materials...
Concept Of Simple Average Method, Its Advantages And Disadvantages
Posted on 00:44 by Unknown
In simple average method, issue price of materials are fixed at average unit price. Simple average is an average of price without considering the quantities involved. The average price is calculated by dividing the total of the rates of the materials in the stores by the number of rates of prices.Advantages Of Simple Average MethodMain advantages of simple average method are as follows:1. Simple average method is very suitable when materials are received in uniform lot quantities.2. Simple average method is very easy to operate.3. Simple...
Friday, 14 May 2010
Concept And Meaning Of Last In First Out (LIFO) Method, Its Advantages And Disadvantages
Posted on 23:12 by Unknown
Last-In-First-Out (LIFO) method follows the principle that the last items of materials purchased are issued at first. The valuation of the materials issued is made according to the latest purchase price of materials. The closing stocks of materials are valued always on the earliest prices of materials. In case of a rising price, LIFO method is suitable because material is issued at current market price.Advantages Of LIFO MethodThe main advantages of LIFO method are as follows1. LIFO method is appropriate for matching cost and revenue.2. LIFO method...
Concept Of First In First Out(FIFO) Method, Its Advantages And Disadvantages
Posted on 22:50 by Unknown
The method in which materials are issued from the stores on a first come first serve basis is called FIFO method. In FIFO method, materials are issued strictly on a chronological order. The units of opening stocks of materials are issued first, the units from the first purchase are issued next and the closing stock is remain in stock always from the latest purchase. The value of the closing stock of materials is at the price of the latest purchase.Advantages Of FIFOFollowings are the advantages of FIFO method.1. FIFO method is easy to understand...
Thursday, 13 May 2010
Methods Of Pricing Materials Issued
Posted on 18:45 by Unknown
There are various methods in use of pricing issues of materials from store. The selection of suitable method is significant from the viewpoint of cost absorbed and consequently on profit. Therefore, the method should be selected in the light of probable effects on profit over a period of years.Material is purchased specially for a job. The material issued is charged to the job at its landed cost. Landed cost include the invoice price, freight, cartage and insurance charges on materials. Issue of such items can not be linked with a particular 'lot'...
Meaning, Functions And Advantages Of Perpetual Inventory System
Posted on 18:25 by Unknown
Meaning of perpetual inventory systemPerpetual inventory system is also known as "Automatic Inventory System". Perpetual inventory system is a technique of controlling stock items by maintaining store record in a manner such that stock balances at any point of time are readily available. The terms 'Perpetual Inventory' refer to the system of record-keeping and a continuous physical verification of stocks, with reference to store records.Functions Of Perpetual Inventory System The main functions of perpetual inventory system are as follows.1. Recording...
Differences Between Bin Card And Store Ledger
Posted on 02:38 by Unknown
Following are the main differences between bin card and store ledger.1.UserBin card is maintained by the storekeeper. Store ledger is prepared by cost accounting department.2. NatureBin card is a record of quantity only. Store ledger is a record of quantities and values.3. PeriodIn bin card, entries are made immediately after each transaction. In store ledger, entries are made periodically.4. PostingPostings are made before a transaction in bin card. Posting are made after a transaction in store ledger.5. Using DepartmentBin card is kept inside...
Store Record Methods Or Recording Of Materials Received
Posted on 02:20 by Unknown
The following are the important store record methods that are used for keeping records of the various items of store.1. Bin CardBin card is also known as a bin tag or stock card. A bin is a place, rack or cupboard where materials have been kept. Quantitative records of receipts, issues and closing balance of items of store are shown in a bin card. separate bin cards are maintained for each item and are placed in shelves or bins or are suitably hung up as it convenient. The bun gives a description, a code number of material, bin number, maximum...
Wednesday, 12 May 2010
Concept And Advantages Of Clasification And Codification Of Materials
Posted on 21:33 by Unknown
Concept And Meaning Of Classification And Codification Of MaterialsClassification and codification of materials are steps in maintaining stores in a systematic way. Materials are classified in such way that storing, issuing and identifying of materials become easy. Generally, materials are classified on the basis of their nature. Materials can also be classified on the basis of quality and utility. For example, materials may be classified as raw materials, consumable stores, components, spares and tools. Thus classifying materials on different...
Concept And Meaning OF Storekeeper And Functions Of Storekeeper
Posted on 18:49 by Unknown
Concept And Meaning of storekeeperA manufacturing company appoints a person for careful storing and safeguarding materials in a store who is called storekeeper. A storekeeper is a person who is the chief of stores and who is given the responsibility of store management. Storekeeper is responsible for safeguarding the materials and supplies in proper place until they are required for production activities. A storekeeper should be well-experienced, well-trained, honest and familiar with the tricks of store-keeping.The main functions of storekeeper...
Selection Of The Location Of Stores
Posted on 00:40 by Unknown
Location of stores means the place where the stores are situated. The location of stores should be carefully planned for a maximum efficiency. Store should be located near the materials receiving departments and materials user departments. The following factors are important for deciding the location of the store.* Heavy and bulky items should be stocked very close to user department.* The store should be located near a road or railway.* The receiving department should also be in proximity to the store god owns* The store should be centrally situated...
Concept And Meaning Of Central Store With Sub-stores,Its Advantages And Disadvantages
Posted on 00:23 by Unknown
Concept And Meaning Of Central Store With Sub Stores This is a mixed store system, a mix of centralized and decentralized stores. Under this store system, sub-stores are established in different departments according to the requirement of the company. Sub-stores are maintained at each department when the central store is at a distance from the production department. Such sub-stores are managed and controlled bu the central store itself. At the beginning of a period, the central store issues a fixed quantity of materials to the sub-stores. At the...
Tuesday, 11 May 2010
Meaning Of Decentralized Store, Its Advantages And Disadvantages
Posted on 21:41 by Unknown
Meaning Of Decentralized StoresA decentralized store is that type of store which receives materials for and issues them to only one department and not to the whole company. The decentralized store may be in many numbers in the company, as each department has its own such store. Purchasing and handling of materials are undertaken by each and every department separately. If the volume of material activities is large, this type of store is suitable because each and every branch has their own store for facilitating smooth operations of their production...
Meaning Of Centralized Store, Its Advantages And Disadvantages
Posted on 21:26 by Unknown
Meaning of centralized storesA centralized store is that store which receives materials for and issues them to all departments, divisions and production floors of the company. Such a store is only one in the company which receives materials for and issues to all who need them. The materials required for all the departments and branches are stored and issued by only one store.Advantages Of Centralized StoresThe followings are the main advantages of centralized stores.1. A better supervision of store is possible because the store is located under...
Monday, 3 May 2010
Concept And Meaning Of Store-keeping ,Its Objectives And Types Of Stores
Posted on 03:15 by Unknown
Concept And Meaning Of Store-KeepingA store refers to raw materials, work-in-progress and finished goods remaining in stock. Store-keeping means the activities relating to purchasing, issuing, protecting, storing and recording of the materials. Store-keeping includes the receipts and issues of materials, their recording, movements in and out of the store and safeguarding of materials. The store is a service department headed by a store-keeper who is responsible for a proper storage, protection and issue of all kinds of materials.Objectives Of Store-keepingThe...
Material Purchasing And Receiving Procedures
Posted on 02:39 by Unknown
Purchasing of materials involves a number of steps, which may be different from one company to another. Generally, following steps are involved in purchasing and receiving materials.1. Purchase RequisitionA purchase requisition is a formal request initiated by the store-keeper. The purchase requisition can also be initiated by other departments for purchase of special items not normally stocked. With the help of purchase requisition, the purchase manager comes to know the types of materials required for different departments. Generally, printed...
Saturday, 1 May 2010
Concept And Meaning Of Decentralized Purchasing, Advantages And Disadvantages Of Decentralized Purchasing
Posted on 20:27 by Unknown
Concept And Meaning Of Decentralized Purchasing Decentralized purchasing refers to purchasing materials by all departments and branches independently to fulfill their needs. Such a purchasing occurs when departments and branches purchase separately and individually. Under decentralized purchasing, there is no one purchasing manager who has the right to purchase materials for all departments and divisions. The defects of centralized purchasing can be overcome by decentralized purchasing system. Decentralized purchasing helps to purchase the materials...
Concept And Meaning Of Centralized Purchasing,Its Advantages And Disadvantages
Posted on 20:03 by Unknown
Concept And Meaning Of Centralized Purchasing Centralized purchasing refers to the purchase of materials by a single purchase department. This department is headed and managed by a purchasing manager. Under centralized purchasing, all purchases made by the purchase department to avoid duplication, overlapping and the non-uniform procurement. A company has to follow the centralized purchasing of materials for ensuring proper materials control as well as efficient store keeping. Under this system, the purchasing department purchases the required...
Concept And Meaning Of Purchasing And Purchase Control
Posted on 19:30 by Unknown
Concept And Meaning Of PurchasingPurchasing involves acquiring materials of right quality, at the right quantity, at right time from a right source and at a reasonable price. A separate purchase department should be established to perform purchasing activities. The size of purchasing department depends upon the quantity to be purchased by the company. The purchase department determine the quality, quantity, items,price and time of purchase of materials. The function of purchase department is to purchase materials , supplies , machines and tools...
Subscribe to:
Posts (Atom)